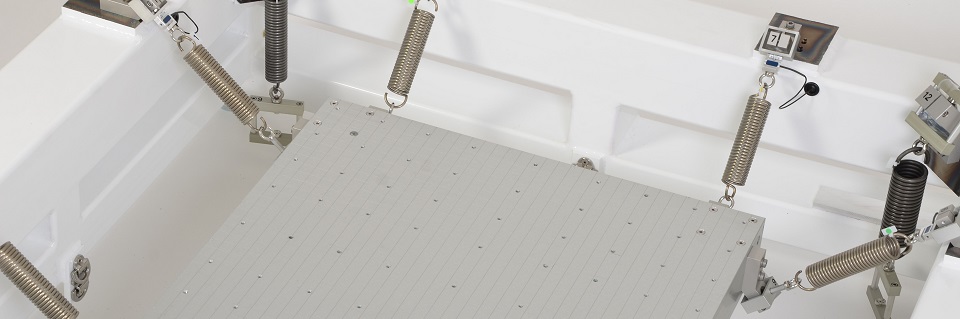
Resonic S 
高精度、短時間で計測する柔軟性の高い測定器
RESONIC Sは、計測対象物を搭載・固定するためのコイルばねで吊るされた水平の計測プラットフォームと、剛性の高いサポートフレームから構成されています。
計測対象物を計測プラットフォーム(台座)に固定し、手で加振します。ロードセルが6自由度の自由振動を測定し、RESONICソフトウェアに転送します。計測対象物をプラットフォームに一度固定すれば、計測完了まで再配置は不要です。
エンジンブロックのような車両コンポーネント部品、バイク等の測定に適しています。
計測対象物の形状、重量に応じて、カスタマイズ致します。
剛性の高いサポートフレーム、コイルばね、計測プラットフォームから構成されます。サポートフレームの内側に、ばね定数が既知の複数のコイルばねによってプラットフォームが吊るされています。
コイルばねは、8つのセンサー付きの計測用ばねと,いくつかのセンサーが装着されていない荷重を支持するためのばねとの2種類があります。計測対象物の重量によって、使用するばね構成を決定します。
ステップ1 計測ジグを用いて、計測対象物を計測プラットフォームに搭載・固定します
ステップ2 計測対象物と計測ジグ、一体状態の慣性特性計測を行います
ステップ3 アーム式三次元計測器等を用いて寸法計測を行います
計測対象物固有の座標系における慣性特性を算出するために必要な工程となります。
ステップ2で一次的に出力されるデータは、計測器上に定められた座標系における慣性特性データ
となります。そのデータを、計測対象物固有の座標系における慣性特性へ変換するために、計測器と
計測対象物の位置関係を計測します。
ステップ4 計測対象物のみをプラットフォーム上から下ろし、計測ジグ単体の慣性特性計測を行います
ステップ5 RESONICのソフトウェアが慣性特性を計算します